At Phoenix Display we understand that your display project is one-of-a-kind. We've compiled some of your commonly asked questions and our answers in this Q&A blog.
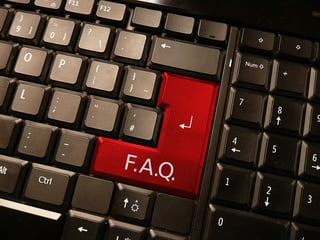
Question: How do I know what kind of display I need and will you help me?
Answer:
Of course we can help you and we are happy to do so! In this situation it’s best to speak with someone so we can better understand your unique situation and offer the best advice on how to proceed. Before getting started it’s important to make sure you are clear on your ideal end product. In our development process we start with the end in mind. Much like how movies are made, we start with your end product, and from that product we learn what you are trying to accomplish with the display.
Also we need to understand who your customers are and how they will be using and interacting with your product. With that information we can determine the type of content needed from the display, and the correct LCD display technology to get the desired optical performance. After that, we work with the LCD design and your product to integrate the two into the most effective and cost efficient manner possible. You can read more here to provide further information on the type of displays to consider.
Question: Can you put a touch panel on any display?
Answer:
For the majority of displays, yes we can! Touch panels are a responsive piece of hardware that cooperate with the application software on the back end completing the LCD display panel product.
There are some limitations to consider which involve the size of the touch panel. Generally smaller displays, 2” or less don’t offer enough space for the user to interact with the touch panel surface and functionality is less than optimal.
Question: What is the typical product life cycle of a display, and how do you handle obsolescence?
Answer:
The general life cycle of our customers’ products runs between 5 and 10 years. LCD display lifecycles depend on a few critical factors, including IC availability, TFT glass availability, unique component availability, and general trends in LCD display technology.
We mitigate the problem of LCD display obsolescence in our development and production process by starting with only readily available components that are not at end of life risk. We then manage each customer’s configuration separately so that a change to one customer’s configuration does not affect another. Obsolescence will not be initiated from our company as long as the part is still in demand.
Monochrome display components generally have multiple sources or can be completely replicated should the original component supplier go end of life. LCD controller components can offer the greatest challenge, but that component often has drop in replacements that allow for a 100% compatible replacement.
The TFT market can also present a challenge as we don’t control the TFT LCD glass or the LCD controller IC. Our ability to source common TFT glass platforms from multiple foundries allows us to have options in the event of a TFT LCD no longer being available.
Step one is designing for obsolesce mitigation in the upfront design. Step two is managing obsolescence when it occurs. Our goal is to support the configuration for the entire life of the project. We will manage the obsolescence process should it occur. We will notify you of all changes as soon as they become available, while providing an ongoing solution though a similar or identical component and the associated redesign. The whole objective is to minimize the impact to the end customers. Throughout this process we avoid any gap in supply and our mission is to prevent any risk to our customer’s production.
We also have many short videos answering our FAQs here and an additional Q&A blog here. Offering solutions and helping our customers with their desired end result is what we love to do. Hopefully you found this Q&A helpful and informative. If you have any additional questions about a current or future product or display, please contact us today.
Photo courtesy of Photosteve101